|
Site-Info: Editorial > Coaster Basics > Typhoon > Wie entsteht eine Achterbahn: Seite 12 |
|
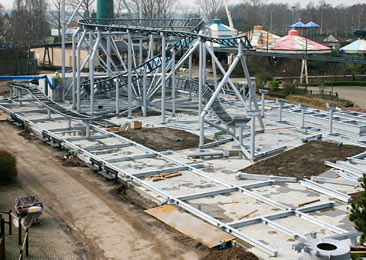 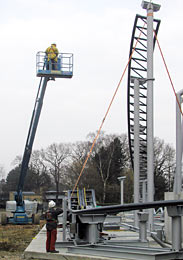 |
Links: Der Montageplatz im Überblick: Das
Aufbauteam startete mit der Station, dann folgte die erste Helix und man
arbeitete sich sukzessive zur gegenüberliegenden Seite vor |
Die Aufgabe war klar definiert: Binnen vier Wochen sollte auf
dem Betonfundament im Bobbejaanland die Achterbahn Typhoon aufgestellt werden,
Verkabelung, Inbetriebnahme und Abnahme durch den DNV inklusive. Die
vorausgegangenen Justierarbeiten, Testfahrten und die TÜV-Abnahmeim Werk
sollten diesen engen Zeitplan möglich machen. Anfang März 2004
startete das Aufbauteam von Gerstlauer im Bobbejaanland mit den umfangreichen
Arbeiten.
"Jeder Aufbau einer Achterbahn ist ein logistisches
Meisterstück", sagt Erwin Haider. 280 Tonnen Gesamtgewicht werden
für Typhoon nach Belgien transportiert. Auf dem Transportweg
zwischen Münsterhausen und Lichtaart erhalten die Schienen und
Stützen in einer Lackiererei in Belgien ihren finalen Farbanstrich. "Die
Herausforderung im Bobbejaanland lag vor allem an den engen
Platzverhältnissen um das Betonfundament", erläutert Erwin
Haider die Situation. An der Nordseite der Achterbahn blockierte alleine
der mobile Kran sämtliche Zufahrtsmöglichkeiten. Daher wurden die
angelieferten Schienen- und Stützenelemente auf einem angrenzenden
Parkplatz abgeladen, zwischengelagert und je nach Bedarf mit einem
Sattelschlepper oder Stapler zum Bauort gebracht.
Für den Nachschub sorgte das Spezialistenteam der Firma
RCS, welche mit einem eigenen Kran die Transporte ablud und just in time
die Stahlelemente dem Aufbauteam von Gerstlauer direkt an der Achterbahn
übergab. In diesem Transportkarussell entpuppte sich die Lackiererei in
Belgien als regelrechter Flaschenhals: Trotz minutiös ausgearbeiteten
Auslieferungsplänen wurden beispielsweise die falschen Elemente geliefert,
sodass zwar die Schienen für den abschließenden Bauabschnitt bereits
vor Ort waren, das Aufbauteam aber durchaus Stunden, wenn nicht Tage, an
einigen Teilabschnitten der Achterbahn auf die nächsten Teile warten und
notgedrungen pausieren musste. "Just in time Installationen sind immer eine
besondere Herausforderung," resümiert Erwin Haider. Hatte man
anfangs ein kleines Team auf der Baustelle, wurde in den letzten Montagetagen
aufgestockt. Pünktlichkeit ist im Vergnügungsgewerbe eine
entscheidende Erfolgskomponente. |
|
Der Ablauf des Aufbaus war durch die aus mehreren Ebenen
bestehende Struktur der Bahn nebst der relevanten Systemschienen vorgegeben:
Erst wurde der Stationsbereich fertiggestellt, um mit dem elektrischen
Anschluss der Reibradmotoren beginnen zu können, dann folgten die
Schlussbremse und die Helix am Fuße der Station. Anschließend
arbeitete sich das Gerstlauer Team in Richtung der beiden Blockbremsen
am gegenüberliegenden Ende der Anlage vor und komplettierte den Liftturm
nebst Vertikallooping.
Die Montagearbeit lässt sich dabei prinzipiell in drei
voneinander getrennte Abschnitte gliedern, die parallel zueinander ablaufen
können: Erst wird die Sohle gelegt, dann die Stützen und Schienen
stückweise miteinander verschraubt und schließlich folgt das Finish
der Schienenstöße nebst dem Anschluss und Testen der mechanischen
und elektrischen Komponenten.
Der Montageabschnitt der Stützen und Schienen nahm rund drei
Wochen in Anspruch: Durch die engen Platzverhältnisse wurden die einzelnen
Komponenten auf einem Sattelschlepper vom Parkplatz zum Navigationsbereich des
Krans gebracht. Die größeren Stützelemente wie zum Beispiel die
A-Böcke (eine Kombination aus einer vertikalen und einer schrägen
Stütze) werden untereinander am Boden verschraubt. Anschließend wird
die einzelne Stütze oder der gesamte Stützenbock auf der Sohle
montiert. Um die Lackierung nicht zu beschädigen, werden die Stahlemente
mit Hölzern unterlegt. Trotzdem lassen sich kleine Schäden am Lack
nicht gänzlich vermeiden. Das sogenannte "Touch Up Painting" am Ende der
Installation behebt diese Lackschäden wieder. |
|
|
|
|
|
|
Jedes Stahlteil ist nummeriert und üblicherweise mit der
Fahrtrichtung gekennzeichnet. So lassen sich falsch platzierte Stützen
vermeiden, denn die Flanschanschlüsse sind derart vorgefertigt, dass
Schiene und Stütze nur in einer ganz bestimmten Ausrichtung zueinander
gefügt werden können. Die Verbindungsstelle ist als Flansch mit zwei
ebenen Flächen nebst einem miteinander korrespondierenden Bohrbild
ausgelegt.
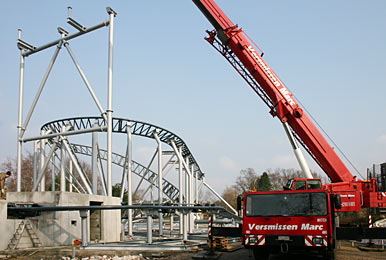 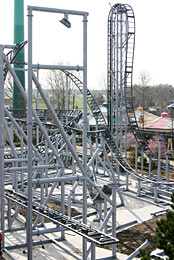 |
Links: Die Nordseite der Bahn war schwer
zugänglich |
Dabei müssen die Verbindungsflächen passgenau
gefügt werden. Klaffende Lücken an den Flanschen würden sich
negativ auf die Kraftübertragung auswirken. "Es kann schon einmal
vorkommen, dass der im Raum auszurichtende Stützenkopf falsch im Werk
geschweisst wurde," sagt Erwin Haider. Für derartige
Eventualitäten ist man jedoch vorbereitet: Falsch geschweißte
Stützenköpfe werden am Rohr getrennt, neu ausgerichtet und wieder
festgeschweißt.
Nachdem die Stütze provisorisch auf der Sohle befestigt
wurde, kann das 2-3 Tonnen schwere Zweigurtelement montiert werden. Dazu wird
die Schiene mit Kettenzügen derart austariert, dass diese für den
Einbau am Schienenstoß in luftiger Höhe korrekt ausgerichtet ist.
Dieser wichtige, iterative Prozess findet am Boden statt und ist der
Schlüsselvorgang für eine schnelle und einfache Installation der
Schiene.
Anschließend wird die Schiene an die Position gehoben, wo
sie mit Muskelkraft von den Arbeitern auf der fertigen Struktur und im Korb
sowie von Zugseilen am Boden aus millimetergenau ausgerichtet wird. Die
Schienenverbindungen, die sogenannten Schienenstöße, bestehen aus
einem Lochbild nebst zwei in den beiden Schienenrohren eingebrachten
Steckverbindungen, welche den Montagevorgang durch ihre Zentriereigenschaft
erleichtern. Das eine Schienenrohr besitzt ein zylindrisches Steckerelement,
während das Schienengegenstück eine Vertiefung aufweist. Nach
Ausrichtung der am Kranhacken hängenden Schiene werden die
Verbindungselemente miteinander gefügt. Dabei werden der glatte
Übergang der Laufflächen geprüft und anschließend die bis
zu 25 Zentimeter langen hochfesten Schrauben festgezogen. Jede Schiene weist
dazu an den Stoßstellen eingeschweißte Büchsen auf, durch
welche die Schrauben gesteckt und die Muttern mit hohen Drehmoment angezogen
werden. Besonderes Augenmerk wird vor allem dem Übergang von Schienenrohr
zu Schienenrohr gewidmet, entscheidet dieser schließlich über
spätere Fahrqualitäten. Knicke oder ein Versatz sind beim
Schienenstoß zu vermeiden. Zwar wurden die Schienenübergänge
bei der Fertigung und dem Probeaufbau geschliffen, doch Montagetoleranzen
erfordern durchaus geringfügige Nacharbeiten. Schleifmaschine und Flex
gehören dabei zur Ausstattung der Arbeiter. |
|
|
|
|
|
|
|
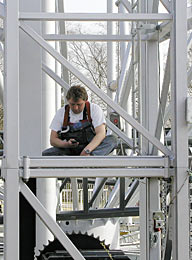 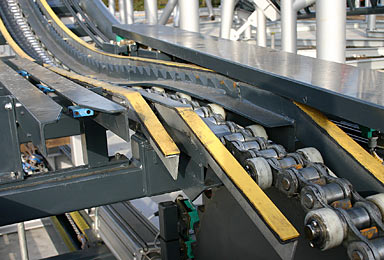 |
Die aufwendige Liftmechanik will vor der
Inbetriebnahme montiert, justiert und geschmiert werden |
Schon beim Zusammenbau der Stahlteile begannen die
Gerstlauer Mechaniker mit der Montage der Elektrokabel,
Luftschläuche und dem Einschmieren der mechanischen Verschleißteile.
Die Bremssegmente waren vom Werk aus komplett vormontiert, sodass die Montage
vor Ort entfallen konnte. War anfangs nur ein vierköpfiges Team im
Einsatz, wurde dieses über die nächsten vier Wochen verdoppelt,
sodass die Bahn zum anvisierten Eröffnungstermin Anfang April
betriebsbereit hätte sein können. "Nur der Treppenabschnitt zur
Bremse oberhalb des Stationsdaches fehlte noch", sagt Erwin Haider von
der Firma Gerstlauer. "Aufgrund des noch nicht installierten
Stationsdaches musste dessen Montage noch warten." Lieferung und Aufbau "Just
in time" und doch keine pünktliche Eröffnung. Das vom
Bobbejaanland zu komplettierende Stationsdach ließ etwas auf sich
warten. Daher präsentierte sich der Einstiegsbereich bei der
Publikumnspremiere am 10. April 2006 eher provisorisch..
Für das Bobbejaanland lag die Eröffnung trotzdem
noch vollkommen im Zeitplan, konnte Typhoon doch weit vor der
Hauptsaison in Betrieb genommen werden. Seitdem beeindruckt die Loopigbahn
Parkgäste und die konkurrierenden Mitbewerber, welche sich einen kleinen
Abstecher nach Lichtaart nicht entgehen ließen. |
|
|
|
|
|
|