|
Site-Info: Editorial > Coaster Basics > Typhoon > Wie entsteht eine Achterbahn: Seite 6 |
|
Schon parallel zur Konstruktion von Typhoon starteten im
Frühjahr 2003 die ersten Fertigungsabschnitte. Der Zeitrahmen war eng
gesteckt, und so liefen die Arbeiten in den Werkshallen der Firma Gerstlauer
und ihren Zulieferen zwischen Sommer und Winter 2003 auf Hochtouren. Bremsen,
Fahrzeuge, Antriebe und Schienenelemente wurden produziert und
montiert.
Wie bei jeder Achterbahn ist Stahl der wichtigste
Grundwerkstoff, der praktisch bei jeder Komponente verbaut wird. Stahl gibt es
in allen Variationen: Ob als einfachen Baustahl oder hochfesten und dynamisch
beanspruchbaren Einsatzstahl für Wellen, Kupplungen oder andere
hochbeanspruchte Fahrzeugteile. Eine Stahlachterbahn benötigt
Hunderte von Tonnen, die für das Endprodukt zu bearbeiten sind. Diese
werden auf dem Weltmarkt in den verschiedensten Erscheinungsformen angeboten:
Nahtlose Rohre werden für die Schienen verwendet, Stahlplatten für
die Fahrzeuge und Gussteile für komplexe Bauteilformen.
Mit der CNC-Maschine (Computerized Numerical Control) wird das
Halbzeug (so der Fachbegriff für das erworbene Zwischenprodukt) in Form
gebracht, die Biegemaschine sorgt bei Schienenrohren für die richtigen
Krümmungswinkel und mittels unterschiedlicher Fügemethoden werden die
einzelnen Bauteile des "Puzzles Achterbahn" zu einem Ganzen
zusammengesetzt. |
|
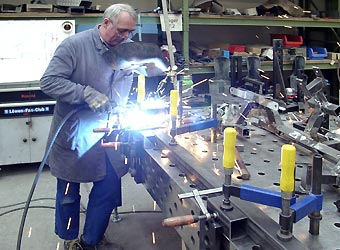 |
Das Stahlchassis wird geschweißt |
Eine Achterbahn verlangt höchste Präzision.
Gewährleistet wird diese durch eine sorgfältige
Qualitätskontrolle. Hochbelastete Bauelemente wie Radschilde oder
Kupplungen werden bis zu ihrer Endmontage mehrfach geprüft. Schon die
Qualität des angelieferten Materials wird von Seiten des Zulieferers durch
Zeugnisse garantiert. Die Prozesskette setzt sich durch Untersuchungen der
Schweißnähte mit Ultraschall oder Oberflächenrissprüfungen
fort. Dem Zufall wird im Achterbahnbau nichts überlassen. Dies geht sogar
soweit, dass jede Schraube mit einem vom Konstrukteur berechneten Anzugsmoment
angezogen und mit einem Lackstrich als "montiert" gekennzeichnet wird. Erst
dann ist garantiert, dass die Verbindung den dynamischen Beanspruchungen
standhält. Die dazu notwendigen Anweisungen sind in den
Fertigungszeichnungen dokumentiert - Ein Papierwust, der die akribische
Präzision "made in Germany" erst ermöglicht.
Wenn die Bauteile die Qualitätskontrolle passiert haben, geht
es in die Lackiererei. Es riecht streng, was auch mit den hier gelagerten
glasfaserverstärkten Kunststoffelementen zusammenhängt. Die
Herstellung der Fahrzeugchassis ist immer noch reine Handarbeit. Erst wird ein
1:1 Holz- und Gipsmodell der Fahrzeughaube angefertigt, dann die Negativform
abgenommen, in der schließlich die 5-10 mm starke Karosserie laminiert
wird. Das robuste Verbundmaterial GFK besteht aus einem ausgehärteten
Polyesterharz mit eingelegten Glasfasermatten. Ein flüssiger Härter
startet den Verfestigungsprozeß, der eine Verarbeitungszeit von etwa
einer halben Stunde zulässt. Die getränkten Glasfasermatten werden in
die Form gelegt, angedrückt und verdichtet. Weitere Schichten werden
hinzugefügt, bis die geforderte Dicke erreicht ist. Innerhalb von 24
Stunden ist das Material derart ausgehärtet, dass es der Form entnommen
und bis auf etwaige Ausbesserungsarbeiten mit Schmirgelpapier direkt seine
Lackierung erhalten kann.
Nebenan warten die geschweißten Stahlchassis der Fahrzeuge
auf ihre Vollendung: Die Sitzreihen stützen sich auf eine Stahlstruktur,
die in ihrer Form dem Buchstaben H ähnelt. Die langen Seiten nehmen zu
beiden Enden die Radschilde auf, der Zwischensteg ist durch eine Kupplung
geteilt, um eine Verwindung der beiden Fahrzeughälften in engen
Fahrfiguren wie der Heartline Roll zu garantieren. Die GFK
Außenhülle und Sitze werden schließlich nur noch angeschraubt.
Dies erfolgt jedoch nicht, bevor der TÜV München die
Konstruktion einer ausgiebigen Untersuchung unterzogen hat.
Im Moment unseres Besuches werden die Sicherungsbügel
montiert. Die Schulterbügel sind am Ende der Rückenlehne
drehbar gelagert, Hydraulikzylinder sorgen für den sicheren Halt. Den
notwendigen Druck im Ölkreislauf gewährleisten kleine
Stickstoffbehälter. Ein elektromagnetisches Ventil regelt die
Druckbeaufschlagung des Zylinderkolbens: In der einen Ventilstellung sperrt das
System, in der anderen lässt sich der Bügel, respektive der
Zylinderkolben, durch Muskelkraft bewegen. Nur bei Stromzufuhr kann der
Bügel geöffnet werden. Der notwendige Strom wird über
elektrische Schleifkontakte ausschließlich im Stationsbereich geliefert.
Eine zweifache Ausführung des Kolbens gewährleistet eine Redundanz:
Wenn ein Hydraulikzylinder ausfällt, kann der andere den Fahrgast
problemlos sichern. |
|
|
|
Eine Halle weiter, im Stahlbau, warten die Schienenelemente des
Turmaufzuges nebst der ersten Abfahrt auf ihre Vollendung. Hier steht auch die
gewaltige Biegemaschine, auf der die nahtlosen Präzisionsstahlrohre ihre
endgültige Form erhalten. Diese werden in Längen von bis zu 12 Metern
angeliefert und entsprechend den Vorgaben des Ingenieurbüros
Stengel gebogen. Drei im Dreieck angeordnete Rollen - zwei davon
verstellbar - prägen in den einzelnen Bearbeitungsschritten die
Krümmung auf. Immer wieder wird das Schienenrohr durch die Maschine
gezogen und für die Erstellung der räumlichen Kurven sogar mehrfach
über ihren Rohrumfang gedreht. Wie schon die Fertigung des GFK ist auch
das Schienenbiegen reine Handarbeit - auch wenn es weitaus mehr Know How
erfordert.
 |
Schienenbiegen im
Detail |
Über im Dreieck angeordnete
Rollen erhalten die stabilen Stahlpräzisionsrohre ihre endgültige,
dreidimensionale Kurvenform. Dazu wurd das Rohr mehrmals durch die Maschine
gezogen und die mittlere Rolle entsprechend der gewünschten Radien
zugestellt. |
|
|
 |
|
Die Fahrrohre werden schließlich provisorisch auf einer
überdimensionalen Schweißplatte auf einstellbaren
Stützelementen angebracht und so ausgerichtet, dass die die Spurtreue von
1200mm eingehalten wird. Nun werden die Querriegel des
Zweigurtträgers angeheftet, wobei der Schweißer kleine
Schweißpunkte in den Verbindungsfugen zwischen den beiden Hohlprofilen
setzt. Derart provisorisch zusammengefügte Schienepaare werden
anschließend abgelängt und mit dem nächsten Schienenstück
am späteren Stossübergang angesetzt, um den glatten, stetigen
Übergang mittels Flex und Bandschleifer herzustellen. Haben die Schienen
die Qualitätskontrolle bestanden, werden in den Verbindungsfugen der
Stahlbauteile durchgehende Schweißnähte angebracht, um die Teile
dauerhaft miteinander zu verbinden.
Für den Transport über die Straße besitzen
typische Schienenelemente eine maximale Länge von zehn bis elf Metern.
Derartige Elemente können mehrere Tonnen auf die Waage bringen, sind
jedoch auf der Baustelle mittels Kran- und Hubwerkzeugen noch handhabbar.
Schraubenverbindungen an fest definierten Flanschpunkten sorgen für festen
Halt der Schienen- und Stützelemente untereinander.
 |
Das Außengelände wartet auf den
temporären Aufbau von Typhoon |
Rund ein Drittel der Typhoon-Schienen wurden bei
Gerstlauer gebogen und geschweißt, die restlichen Zweigurtschienen
wurden in der Slowakei bei der Firma FKM gefertigt. Die Produktion von
Schienen und Stützen für den weltweiten Achterbahnmarkt ist ein
Standbein des osteuropäischen Stahlbauunternehmens. Mehrere Kilometer
Zwei-, Drei- und Viergurtschienen produziert das Unternehmen jährlich. Zu
den Auftraggebern gehören beispielsweise Intamin, Maurer
Söhne und Mack Rides.
Der schwierigen Auftragslage und den saisonalen Stoßzeiten
zum Spätsommer, Herbst und Winter kann eine ausschließliche
Schienenfertigung am eigenen Standort der Achterbahnhersteller nicht mehr
gerecht werden. Bestes Beispiel ist der niederländische
Achterbahnproduzent Vekoma. Bis zum Jahre 2001 beschäftigte man
über 100 Mitarbeiter in der eigenen Fertigung von Schienen und
Stützen nahe der deutsch/niederländischen Grenze. Als die
Aufträge ausblieben, mussten viele Arbeitsplätze aufgegeben werden,
schließlich wurde die gesamte Fertigung nach Osteuropa und China verlegt,
wo in den Werkhallen der Stahlverarbeiter nicht nur ausschließlich
Achterbahnschienen hergestellt werden. Somit sind die Hersteller
äußerst flexibel und können auf den pulsierenden Markt mit
seinen schnellen Hochs und Tiefs reagieren.
Unweit der Schienenfertigung im Hause Gerstlauer erhalten
die Bremsschienen ihren letzten Schliff. Typhoon setzt auf eine
Kombination aus Wirbelstromsystemen und klassischen Reibbremsen. Letztere
werden von Gerstlauer selbst gefertigt. Luftdruckbeaufschlagte
Pneumatikzylinder schalten die Bremselemente, welche an einem Reibblech
unterhalb des Fahrzeuges angreifen. Die Mechanik will justiert und die
Bremsschiene mit ihren verschiedenen Modulen getestet werden. Dann geht es auch
für diese Baugruppe in Richtung Baustelle. Die befindet sich diesmal nur
50 Meter entfernt auf der großzügigen Freifläche des
Werksgeländes. Da Typhoon auf einer ebenen Sohle ruht, kann die
Bahn komplett in im Werk Gerstlauer Elektro GmbH aufgebaut und ausgiebig
getestet werden. Erst nach erfolgreicher Qualitätssicherung wird sie
wieder in ihre Einzelteile zerlegt, erhält auf dem Weg in Richtung Belgien
ihre endgültige Lackierung und will dort schließlich wieder
zusammengefügt werden. |
|
|
|
|