 |
Josef Herzog is developing the Typhoon car
with support of CAD |
|
"There were just six months to design the first version
of Euro Fighter from scratch", Josef Herzog, engineer at
Gerstlauer, remembers. In spring of 2003 this ride was presented
to the public at BonBon Land, Denmark, and less than 12 months
later the second version will follow. Typhoon uses the same cars,
brakes and drives.
Calculations were done, hundreds of single component graphs made
using a computer aided, technical drawing program - in short CAD -
and suppliers searched. "We studied dozens of product
catalogs and had many talks with potential suppliers before we
found the right chain for our lift tower, for example", says
Siegfried Gerstlauer. For Gerstlauer Elektro GmbH
building a roller coaster is everyday business, for other
companies a very exceptional venture.
A roller coaster wants to be well thought through: Without
production drawings and a documentation of the calculations none
such ride can go into service. Neither can a strict coordination
be missing. So the first step of each project is creating a digest
of the schedule, combining causal contexts and the temporal
workflow: So the track can only be produced as soon as all the
calculations are finished. And for designing the layout a defined
interface between the car and the track has to be agreed on: The
engineers have to clarify which elements and features can be
negotiated by the cars. "Depending on the workload we assign
tasks to external engineering offices", Siegfried
Gerstlauer explains. Regarding the output of six coasters for
the 2004 season - a new record high in the history of the company
- the tasks have to be well allocated to the 30 employees.
|
At the beginning of the design process stands the basic idea
regarding the layout like it was described in the last issue of
this series. Afterwards the design of the car is made, including
construction and engineering of the chassis. Service strength
certificates play a leading role when designing the components.
There is a mathematical stability proof to be adduced for each
component before production can start. The adequate state of the
art is outlined in standards like the Deutsche Industrie Norm
(DIN, German Industry Standard) or the European Norm (EN).
The universal tool for the engineer is the CAD that completely
ruled out the classic drawing board and the tusche box: Changes
can be done much faster using the computer, standard parts like
screws, springs and nuts can be taken from libraries and bills of
material can be derived directly from the drawing. A looping
coaster like Typhoon consists of thousands of single
parts - a really complex "puzzle" making high demands on
the designer. There is no apprenticeship or degree for roller
coaster engineers, this job rather is a mix of interdisciplinary
competencies regarding steel construction, mechanical and
electrical engineering. "Today you work on the cars and
tomorrow's task is to design the sole", Josef Herzog outlines
his areas of responsibility.
After completing the specification of the car the design of the
layout begins. In a first step this happens only regarding the
forces affecting the passengers, being extended to the steel
construction itself in later stages of the process. The engineers
aim to turn the basic idea into a layout that obeys the state of
the art. Stability proofs have to be adduced, safety devices
constructed and components dimensioned and developed. A network of
steel pylons keeps the coaster together and draws the highly
dynamic loads out to the earth. Adequate instructions for the
production can be derived from the mathematical calculations. A
roller coaster is supposed to push the limits and to
comply with the safety standards at the same time. Safety is put
in capital letters when building amusement rides, so the
manufacturers cooperate with TÜV from early on,
starting at the first development phases. |
 |
Overview Design - From sktech to final
production datas |
The layout is the geometrical sketch of
the track. It shows the exact sequence of the ups and
downs and the inversions. The graphics consists of a
ground view and an unwind of the track. |
 |
Ground view: Track and heartline are
shown - Maximize with left click |
The ground view shows the track layout by
aerial view. The unwind of track shows the track
unrolled in a plain view. Especially the height
progression is visible. Also technical information
(inclination, distance of columns, ...) are given.
|
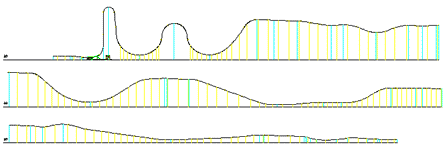 |
Unwind of track - Maximize with left
click |
The 3D-layout is a combination of ground
view and the unwind of track. It is used to visualize
the track layout and does not consist of technical
information. |
 |
3D-layout - Maximize with left click |
The layout is part of the design process
and the cinematic/kinetic result of the track
calculation and configuration. This field of activity
- called dynamics - considers speed, accecerations and
forces (e.g. created by acceleration of train).
Stengel engineering office makes the calculations in
relation to the riding people, the car and the track
to appoint the maximum forces. This calculation is the
basis for the force compatibility for the riding
people and the design of steel structure. |
Nex to layout and dynamics, the static is
the third sub area of roller coaster design. The
column constuction and the steel sole is designed to
absorb the dynamic and static forces - sometimes
multiple tons - and the self-weight of the steel
structure. |
|
 |
|
 |
Werner Stengel |
|
The efforts regarding safety are shared by the Stengel
engineering office in its history of almost 40 years: The graduate
civil engineer Werner Stengel is called "Master of
horror" and was involved in around 600 roller coasters
worldwide. The field of activity of his team, consisting of ten
employees, comprises the exact design of the layout on the basis
of dynamics calculations, includes statics and the computation of
the foundation loads. Gerstlauer, too, avails the services
of the Munich-based engineering office that has worked for all
renowned coaster manufacturers.
The starting point of all considerations regarding Typhoon's
layout was the rough design of the sole and the unwind of the
track, two points the wire model for the presentation at the trade
shows was based on. "Our vision is clearly defined by giving
a layout to the Stengel engineering office", Siegfried
Gerstlauer tells us. "In addition, there were pilot
surveys regarding the car prior to the allocation of the project,
determining the maximum forces and the minimum track radii."
A clear interface definition fixes the cooperation from the
beginning: "The further design of the cars as well as the
layout have to adapt to that", Siegfried Gerstlauer
comments.
Engineering office Stengel optimizes the track at the
computer, using elaborate numerical algorithms to keep the forces
on the passengers below a limit. Every change in direction causes
an acceleration ,
and every coaster has lots of them: Bends, drops and inversions
are analyzed to keep them ridable. Stengel can count on an
extensive amount of experience. Keywords like heartline
and spline
curves
play a lead role when finding the ideal position of the track in
space.
The amount of data is so huge that it can only be handled by
self-made software - The calculations for Typhoon would need
57.000 pieces paper. "Without the use of computers roller
coasters couldn't be designed nowadays", Andreas Wild
of the Stengel engineering office tells us. "Especially
the development and implementation of our program for spline
curves enabled us to design coasters running ultimately smooth and
to give precise instructions for the production to the
manufacturer. Regarding the very short development times these
days we have to use highly modern tools to calculate the rides."
More than 3000 hours of work have been done at the Stengel
engineering office just for Typhoon. Here, too, modern
3D-CAD systems help the engineer to sound the limits of biodynamic
tolerances of the passengers. A simulation of the coaster can be
done based on the CAD data, and so the forces and the dynamic
behaviour can be determined way before a prototype has been built.
The roller coaster is virtually assembled early in the design
phase to test functional relations and mechanisms.
The production data (CAD files and other lists) represented by
3D coordinates and production directives for track, supports and
sole are sent to the manufacturer electronically. "In
principle we can start producing directly from the data we get
from the Stengel office. But mostly we adapt the data to
the local factors at the track manufacturer's site", Siegfried
Gerstlauer explains the process. Track production happens,
depending on workload, "in house" or is passed to a
third party. After five months Typhoon was designed to the
last detail, so the steel construction as well as the production
of the cars could start in summer of 2003.
Typhoon - a roller coaster emerges will be continued. Read
and see in our next issue how the single components of the looping
coaster Typhoon have been produced at the Gerstlauer facility.
Many thanks to Gerstlauer Elektro GmbH and Stengel GmbH for
the friendly support on realizing this article. The copyright for
the pictures belongs to the photographers and the Gerstlauer
Elektro GmbH, Stengel GmbH and Andreas Fechner, respectively.
Publishing, distribution and copying without written permission is
strictly forbidden. |