|
|
|
It was supposed to happen right after the last day of the
season, but now it takes place with a delay of four weeks: Looping
Star leaves its ancestral place in the Belgian Bobbejaanland. The
dismantling is executed by the team of Ride Construction Service
(RCS) around the company´s founder Max Eberhard (see the
portrait below) to gain room for the novelty Typhoon.
"A roller coaster can be dismantled or demolished."
says Max Eberhard, and it quickly becomes obvious that he
grants the first option to Looping Star. The track
segments and support beams are pedanticly numbered and brought to
a parking lot for interim storage. Whoever saw showmen building
their rides might think that this is a job for just a few days.
But this is far wrong: "Over the years a tension developed in
the structure, and there is the corrosion, too. From the age of
the ride, the size and the manufacturer you can make a pretty
accurate estimate how long the dismantling will take." we are
told by Ronald Schäfer, the chief of the building
site. In the case of Looping Star this will be two weeks. "We´ve
spent the first five days with preparations." adds Max
Eberhard. "We removed the electrical and hydraulic
components, entry and exit, the station and other smaller parts.
Removing the track and the support structure will take seven days,
and two more days later you can barely see that here once stood a
roller coaster." |
|
 |
. |
 |
|
|
|
Ronald Schäfer and his portable crane |
|
During the first five days most of the screws and bolts were
removed. Many had to be freed from rust and persistant dirt with
an angle grinder and oiled a couple of times before they could be
detached. But the track isn´t any easier to remove. It can
take more than 30 minutes until a piece can be hoisted out with
the crane. "The transitions between the track segments and to
the support beams are pretty seized up. We could loosen most of
them, but in one case we had to use a flame cutter." Max
Eberhard tells us.
The parts are hoisted onto a trailer and brought to the parking
lot. "We have 50 to 60 track segments, and each of them
weighs between 1.5 and 3 tons." Ronald Schäfer
reports. "The large pallets with the brake segments and parts
of the trains reach up to 18 tons." Those parts have to be
lifted with two cranes. And it isn´t coincidental that they
exactly fit on the trailer: "Schwarzkopf was very farsighted
when he built the rides. All the pallets comply with the 44 feet
norm for sea cargo containers, and even most of the track parts
and support beams can be stored on the footprint of 12 times 2.5
meters." Schäfer tells us. So the team of eight
workers removes one element after the other. It isn´t decided
yet what will happen to the coaster. Right now the focus is on
clearing the area in time. |
|
 |
. |
 |
|
|
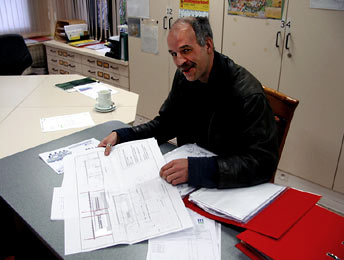 |
Project manager Filip Bogaerts shows Typhoon's
drawings |
|
As soon as the last pieces of Looping Star will be
removed, works on the foundation of Typhoon will begin.
Around 100 piles have to be sunk into the ground. The 10 to 12
meters long concrete cuboids will be delivered by local companies
and have to be handled by christmas. In the new year a 25
centimeters thick concrete slab will be cast over the whole
footprint. "In the beginning we gained some time, but we
directly lost it because of the uncertainty regarding Looping
Star." we are told by Filip Bogaerts, the project
manager responsible for Typhoon. The studied architect and
security advisor is working for Bobbejaanland as an
external consultant since 1988. "But we are on time with all
three attractions. The foundation for the Vekoma junior
coaster is almost done, the construction of the ride itself
will start in the middle of January."
One month later the Giant Frisbee delivered by Huss
will follow, and in the first days of March the works on Typhoon
will begin. The new roller coaster has already taken the first
obstacle: "Lately representatives of Gerstlauer and DNV
were here to conduct the risk analysis." reports Bogaerts.
During this analysis all possible faults are played through
theoretically and the countermeasures are evaluated. Typhoon
passed all tests of the safety engineers of Det Norske Veritas,
the Norwegian equivalent to German TÜV, with flying
colors. The next steps will be the TÜV approval and
the first test runs on the site of Gerstlauer Elektro GmbH.
Coastersandmore.de will also report on this in the
continuation of this article series. |
|
 |
. |
 |
|
|
|
Left: The friends Ronald Schäfer and Max
Eberhard |
|
In 1999 Max Eberhard, born in 1975 and showman in the
8th generation, founded the company RCS. That year the
roller coaster company Vekoma from the Netherlands sold
the traveling ride Evolution owned by his father to Six
Flags Great Adventure in the United States and was looking for
somebody do construct it there. Eberhard realized that he
found a gap in the market and specialized in constructing and
dismantling roller coasters and other rides - in a time when many
manufacturers sourced out subtasks like steel construction or the
assembly of the attractions.
One year later Ronald Schäfer, who can look back on
20 years of experience as a showman, joined in. The two friends
are a well-rehearsed team: While Eberhard is responsible
for order acquisition, administration and establishing the
construction sites, Schäfer´s job starts on
location: "We trust each other blindly!" they tell
unanimously. They have a permanent staff of 15 workers. Each of
them has his special subject, from welding and electrical
equipment to precisely shunting the trailers. "But we already
had up to 36 people on different sites at the same time."
says Max Eberhard. His team has constructed more than 50
rides worldwide so far.
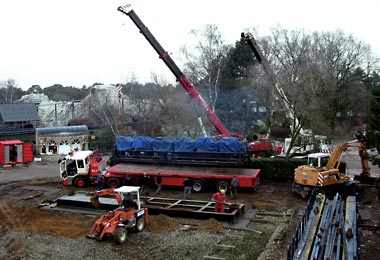 |
Overview |
|
Besides reliable and experienced workers especially the
equipment is the vital asset of RCS. Apart from two
30-ton-cranes there is a HIAB on an own truck available.
One of the cranes is equipped with an additional unit for cage
usage, and the HIAB was upgraded with a wireless remote
control. In addition, there are four trucks and four trailers. To
complete the pool RCS owns two magazine containers and two for
tools. "I have a tool fetish." Eberhard declares
with a broad grin. "There is no special tool in our field we
don´t have." One of those is a special press that
locates the track segments in position for bolting them together,
or a device to burst non-detachable nuts without damaging the
screw thread. "We inspect and repair our vehicle fleet
ourselves. And I set a high value on the appearance of our
equipment."
If there is a ride to construct, the manufacturer or the new
owner contacts RCS. Considering the constructional drawing
a time schedule and a cost estimate are made. "The plans can
be called my homework." says Ronald Schäfer. "On
my desk there is already a roller coaster for the US." More
can´t be drawn from him. "Our clients expect reticence
as well as professionalism on construction." And that is what
they get. |
|
Many thanks to the team of Ride Construction Service and
Bobbejaanland BV for the friendly support on realizing this
article. The copyright for the pictures belongs to the
photographers and Bobbejaanland BV respectively. Publishing,
distribution and copying without written permission is strictly
forbidden. |
|
|
|